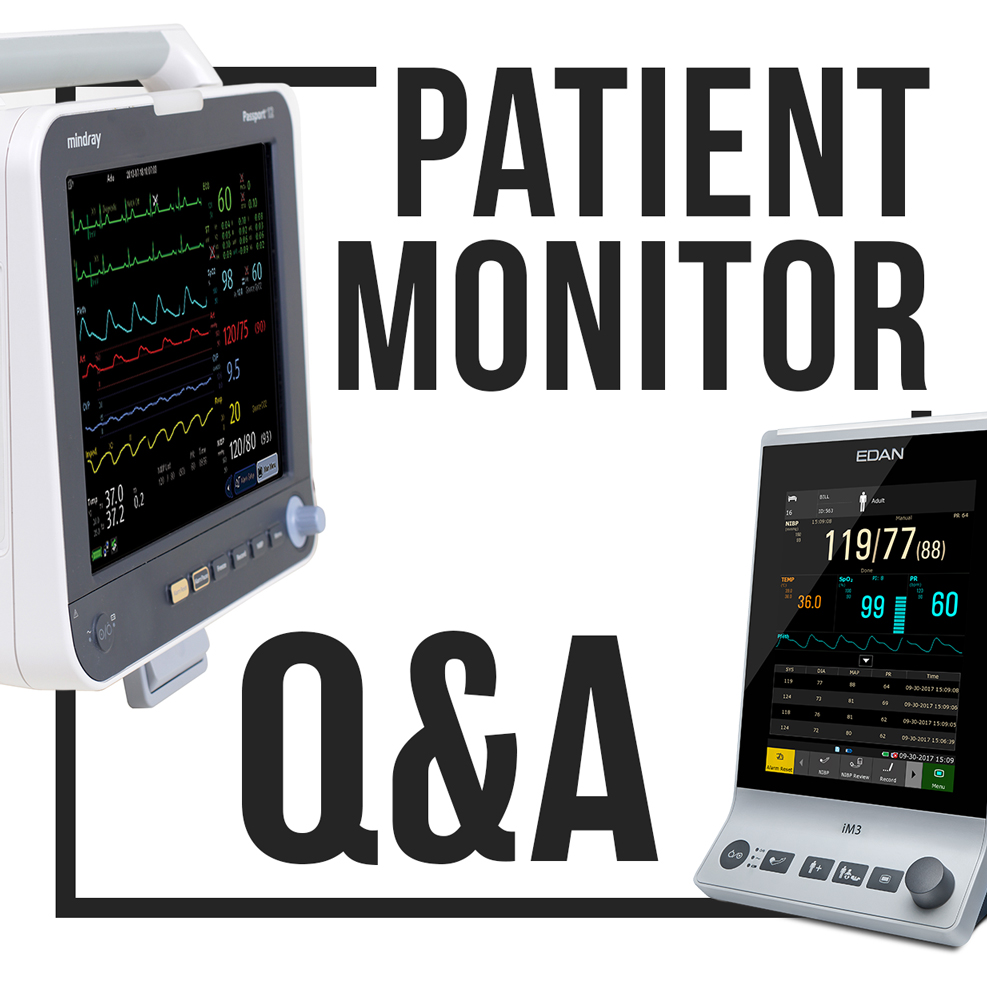
TechNation Invited several industry leaders to share their insights regarding patient monitors in this roundtable article. Neil Davidson, Director of Biomedical Services at ReNew Biomedical, answered questions regarding some new features HTM professionals should be aware of as well as cybersecurity concerns and more.
Q. What are some new features biomeds should seek out when a facility purchases patient monitors?
Neil Davidson: Data transmission is important on any new piece of equipment. Assuring that the unit’s software is compatible to EMRs is always pertinent when preparing for a change. New technology displays are featuring useful reporting capabilities for service technicians. Ask for a sample of the reporting technology. These “smart” units have the ability to tell you what is wrong and where to look first. Both are helpful when the units are desperately needed and you are in a time crunch. Remember to ask questions such as: Is it easy to do software upgrades on the units? Is it configurable to meet the needs of the medical practice? Does it have a battery backup and what is the lifespan of the battery? (Be aware that touch screen technology may bleed the lifespan of battery backup.) Touch screen versus button technology may present different challenges too. Is there a simple preventative maintenance plan for the unit or does the unit need a OEM-certified technician to do the work?
Q: What measures should be taken concerning cybersecurity?
Davidson: Nothing could be more underrated than the importance of cultivating a good working relationship with the IT department. Having an open line of communication with the OEM service department will also go a long way to resolve issues fast. Most newer models have software that requires updating periodically. It’s important to follow through on those updates because most manufacturers offer solutions before problems occur.
Q: How can Biomeds help extend usefulness of an older patient monitor?
Davidson: Yearly cleanings of the internal and external components of your units will certainly extend the life. Replacing the coins cells and batteries on a yearly basis or sooner will ensure that there is no unexpected down time. Make sure that your biomedical staff has access to all of the product manuals and each book is open to assist when necessary.
Q: With systems transitioning, how can Biomeds ensure that monitors are compatible?
Davidson: Never underestimate the value of research. Many OEM sales technicians can answer your questions before you sacrifice your budget on a unit that is not compatible with your EMR or other medical devices.
Q: What are the most important things to consider during a PM?
Davidson: Invest in top-quality testing equipment. Do your due diligence and check every box suggested by the OEM when testing. Keep clean documentation and file it away with the product’s serial number and additional materials. Clean the units with safe and gentle solutions. If you are outsourcing your service, make sure that your company of choice is ISO certified. Quality equipment can only stay in excellent condition if it has been serviced properly.
Q: What else do you think TechNation readers need to know about purchasing and servicing patient monitoring devices?
Davidson: Take the time to do your homework and do your best to force the work-arounds of ever-changing technology. Ask about the manual overrides, warranties or OEM service department contact numbers in case they are needed for future use. Saving all of that information in one file folder will go a long way in securing accurate information fast. Don’t forget how valuable that information can be in increasing the resale value of that unit. Consulting your service team when purchasing units will help to answer many unforeseen problems with new equipment. Most technicians have enough experience to assist any buying agent through a necessary equipment purchase. Allowing a service technician and a medical professional to test drive a unit before purchase should answer most questions ahead of time. Renting a new unit can also save money and worry. No one wants to make the wrong decision and many need more information then what the product manual provides.
Neil Davidson
Director of Biomed Services, ReNew Biomedical
Originally published in
February 2020 edition of TechNation.